The humble plastic bucket is an industrial workhorse. What could you possibly do to it to make it better? For one thing, you could make them more durable. Could you do that without adding weight? That’s what I was able to pull off with the Letica Dual-Lock Container. With an in-house testing facility, I was able to study the failure mode of containers, both when they were compressed on one-another and compressed individually. By itself, a container is amazingly strong, but when stacked, the weak point is the lid – so relatively weak that it would collapse with only a quarter of the weight that the container itself could withstand. What stacked containers did was turn the lid inside out which caused the lock to disengage, sending the top container into the bottom one. This was especially problematic when heat caused the plastic to soften. Now picture these containers full of paint in an Atlanta warehouse and you can imagine the mess. They typical solution was to add plastic to where it was most prone to bend. But that can only take you so far until you end up with molding issues and even then it’s really just a band-aid solution.
What I did was create a system that exploited the best attributes of plastic. Where plastic is really strong is in compression. If I could re-direct the rotational forces exerted on the lid into compression it would have a dramatic impact on stacking performance. A big part of the solution was to align the vertical wall of the container with a vertical wall on the lid. That channeled those forces back to the container which was already very strong.
But there was another thing I noticed – when stacked containers were compressed, the groove in the outer wall of the lid there for the tear-off band acted as a hinge. While the outer wall would flare out, the tear band did not. So by moving the locking feature below that groove we could prolong the engagement of the lid with the container adding even more strength.
With the success of these features, I moved on to the problem of sealing. Traditionally, containers used a hollow, rubber O-ring in the lid. That would compress and form a tight seal so if the container were tipped, it would not leak. This worked well but for one all too common scenario. If the container were at the bottom of a stack, the O-ring would be severely compressed and when relieved of the weight above it, that O-ring could take weeks to rebound into shape and perform the way it had initially. That left them vulnerable to spilling. By leveraging the strengths of plastic, I was able to eliminate the O-ring. By making the top of the container curved with a relief underneath, the edge was now able to flex, sort of like an O-ring. With a matching round and slightly smaller profile, the lid mated perfectly to the container top and even though severe compression would cause the lid to slightly rotate, the fact that their profiles were round kept them in constant contact.
Patent #6,688,483


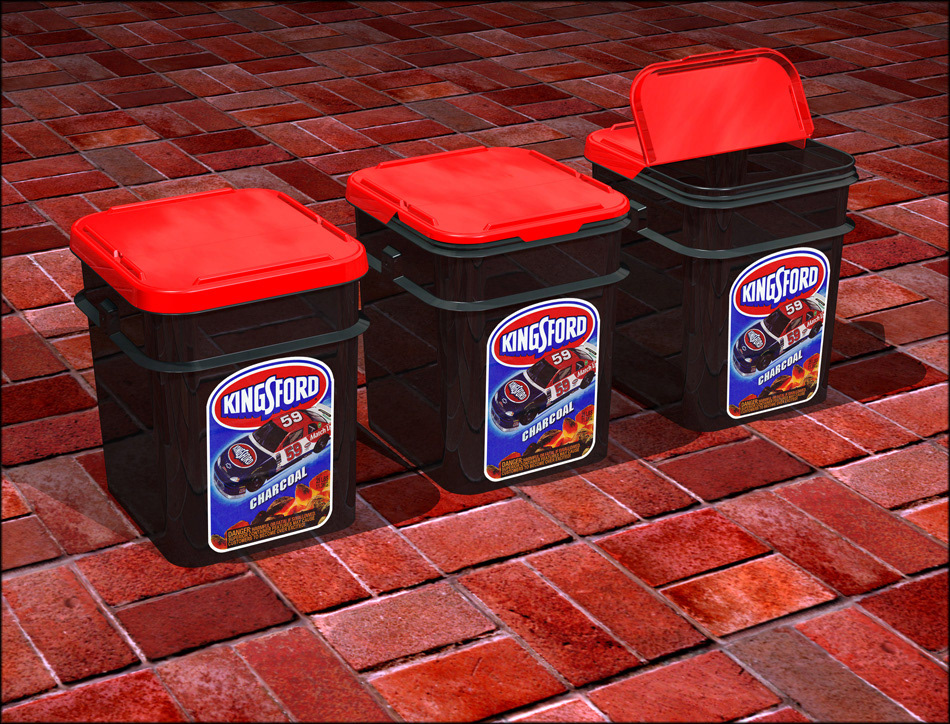